Morrama partners with Batch.Works on adaptable kids’ headphones
A modular design not only allows broken parts to be replaced, but enables the product to “grow” with the child from age five to eleven.
Morrama has collaborated with circular manufacturing company Batch.Works on Kibu, a pair of headphones made using replaceable, recyclable components and designed to be assembled and customised by kids.
The collaboration gave both parties an opportunity to “explore and innovate in the relatively new field of 3D printing”, though each part had to be “carefully designed” to work with the 3D printer bed, says Morrama associate director Andy Trewin Hutt.
The main body of the Kibu headphones comprises 3D-printed filament made from 100% waste PLA (Polylactic Acid), which is a plant-based, biodegradable plastic. The material is collected in the Netherlands and turned into filament by Reflow, a company located nearby to Batch.Works’ production in Amsterdam.
As of now, Kibu’s foam TPU (Thermoplastic Polyurethane) headband is printed with virgin material, but Batch.Works partner and head of research and development Milo McLoughlin-Greening says it has started to “develop a recycled version with [its] supplier partners” that is due to be finished before the first headphones are sold.
Batch.Works’ digital process allows it to “fluidly iterate as [it] goes”, McLoughlin-Greening adds, so when new material options become available, the manufacturer can easily incorporate them, as well as including material generated from its own waste.
While it is more difficult to find circular options when it comes to the electronic components, Batch.Works is working with UK manufacturer Jiva Materials to make a soluble printed circuit board material. The company will be listing the source of each part publicly and explaining its how it fits into the circular lifecycle of the product.
For easy disassembly, the headphones’ eight-part structure fits together without any external fixings. Trewin Hutt credits the success of the design to its simplicity, explaining that fewer parts mean there is less to manufacture and repair.
As the product is targeted at children aged five to eleven, Trewin Hutt says the team increased the size of the parts to reduce the chance of them being ingested.
One of the main drivers of the product is tackling the e-waste problem. While its modular design means that broken parts can be easily replaced, Trewin Hutt says it also allows for the headphones to be adjusted, so they comfortably fit as the child grows.
Research revealed “children often want more mature and premium looking products, especially when it comes to tech”, says Trewin Hutt. In response to this, the studio incorporated “organic surfaces into the geometric forms” compatible with the 3D printer, he explains.
Batch.Works has developed many colours alongside its filament production partner, and the team chose “a neutral yet colourful palette”, Trewin Hutt adds.
The logistical UX system for requesting spare parts is still in development. McLoughlin-Greening says: “A key part of our business model is to manufacture at multiple locations making collection and repairs available as locally as possible to the user”.
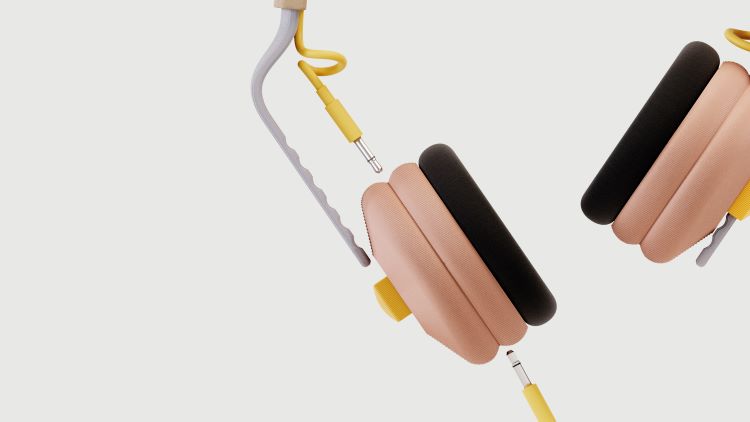
He adds that Batch.Works is currently developing a technique for “embedding an invisible unique part identification into every item we produce, like adding DNA”. This would enable the manufacturer to track exactly which batch and material a part is made from,, facilitating more “data-driven recycling” and “adding a traceable legacy to material as it moves from one form to the next”, says McLoughlin-Greening.
Branding agency Studio Don are responsible for the project’s name and brand identity, foregrounding the idea of the build, repair and recycle process with Kibu, an abbreviation of Kids-Build.
Kibu is currently in the validation phase and undergoing user-testing to refine the design before its launch later this year. Trewin Hutt hints that the Kibu headphones will not be the last product from this joint venture.
-
Post a comment